Introduction
In today’s modern world, electricity is a crucial resource that powers our homes, businesses, and industries. However, the supply of electricity from the grid is not always reliable, especially in areas prone to frequent power outages or where the grid infrastructure is inadequate. In such situations, diesel generators play a vital role in providing backup power to ensure continuity of operations. This article will explore the use of diesel generators for inductive loads, focusing on their importance, working principles, and best practices for optimal performance.
Importance of Diesel Generators for Inductive Loads
Inductive loads are devices that require a sudden surge of power to start or operate, such as electric motors, compressors, pumps, and HVAC systems. These loads pose a unique challenge to power generation systems, as they can cause voltage fluctuations and power surges that may damage sensitive equipment or disrupt operations. Diesel generators are well-suited for powering inductive loads due to their robust design, high reliability, and ability to provide immediate backup power when needed.
One of the key advantages of diesel generators for inductive loads is their ability to handle sudden changes in load demand. When a motor or other inductive load starts up, it can draw a large amount of current for a short period, known as inrush current. Diesel generators are able to respond quickly to these changes in load demand and provide the necessary power to start the inductive load without causing voltage drops or disruptions.
Additionally, diesel generators are known for their high torque output, which is essential for driving inductive loads such as motors and pumps. The steady and reliable power output of diesel generators ensures that inductive loads can operate efficiently and without any issues, even during peak demand periods.
Working Principles of Diesel Generators
Diesel generators operate on the principle of converting chemical energy stored in diesel fuel into mechanical energy, which is then converted into electrical energy through an alternator. The basic components of a diesel generator include the engine, alternator, fuel system, cooling system, exhaust system, and control panel.
The engine of a diesel generator is responsible for powering the generator and is typically a compression-ignition internal combustion engine that runs on diesel fuel. The engine drives the alternator, which is connected to the engine through a shaft and is responsible for converting the mechanical energy into electrical energy. The alternator produces alternating current (AC) electricity, which can then be used to power inductive loads.
The fuel system of a diesel generator consists of a fuel tank, fuel pump, fuel filters, and fuel injectors. Diesel fuel is drawn from the fuel tank by the fuel pump and delivered to the engine through the fuel injectors, where it is combusted to produce power. Proper maintenance of the fuel system is essential to ensure the reliable operation of the diesel generator.
The cooling system of a diesel generator helps regulate the temperature of the engine and prevent overheating during operation. Cooling is usually achieved through the circulation of coolant fluid, which absorbs heat from the engine and is then cooled in a radiator before being recirculated. Adequate cooling is essential to prevent the engine from overheating and ensure the efficient operation of the generator.
The exhaust system of a diesel generator is responsible for removing the combustion gases produced during operation. 1000kw diesel generator for emergency backup pass through a series of pipes and mufflers before being released into the atmosphere. Proper exhaust system design is crucial to minimize noise and emissions from the diesel generator.
The control panel of a diesel generator houses the various controls and monitoring devices that allow operators to start, stop, and monitor the generator. The control panel typically includes features such as voltage and frequency meters, engine gauges, start/stop controls, and safety shutdowns. Effective monitoring and control of the diesel generator are essential to ensure its reliable operation and prevent damage to inductive loads.
Best Practices for Operating Diesel Generators with Inductive Loads
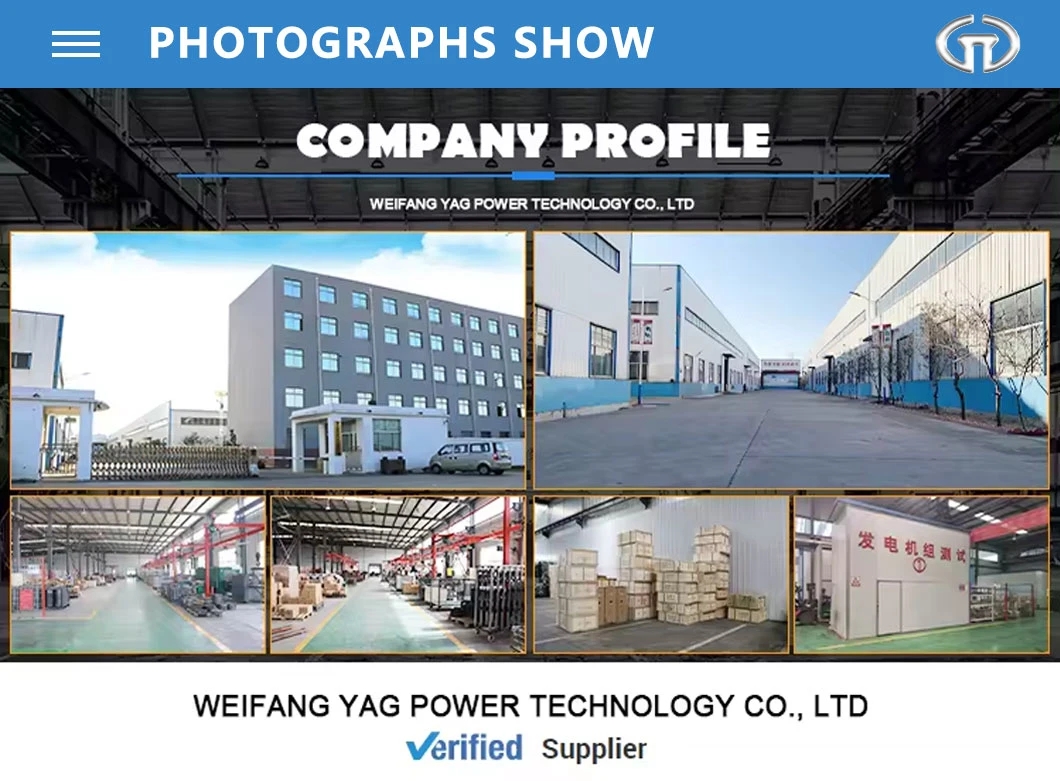
When operating diesel generators with inductive loads, there are several best practices that should be followed to ensure optimal performance and reliability. These practices include proper sizing of the generator, regular maintenance, load testing, and fuel management.
Proper sizing of the generator is crucial to ensure that it can meet the power requirements of the inductive loads without being overloaded. An undersized generator may struggle to start inductive loads or may trip due to overloading, while an oversized generator may be inefficient and lead to increased fuel consumption. It is important to consult with a qualified engineer to determine the correct size of the generator based on the specific inductive loads to be powered.
Regular maintenance is essential to keep the diesel generator in good working condition and prevent breakdowns or failures. Maintenance tasks may include checking and changing the oil, filters, and spark plugs, inspecting the fuel system for leaks or blockages, testing the battery and electrical connections, and ensuring proper ventilation and cooling. A well-maintained generator is more likely to operate reliably and efficiently when powering inductive loads.
Load testing is another important practice for diesel generators to ensure that they can handle the startup and operation of inductive loads. Load testing involves simulating the actual load conditions of the generator by connecting it to a load bank or inductive load and monitoring its performance. This helps identify any potential issues or weaknesses in the generator’s operation and allows for adjustments to be made to improve its performance.
Fuel management is critical for diesel generators to ensure a reliable fuel supply and prevent fuel-related issues during operation. Proper fuel storage, handling, and monitoring practices should be followed to prevent contamination, degradation, or running out of fuel. Regular fuel testing and treatment can help maintain the quality of the fuel and prevent issues such as clogging of fuel filters or injector problems.
Conclusion
Diesel generators play a crucial role in providing backup power for inductive loads in various applications, ensuring continuity of operations and protecting sensitive equipment from power disruptions. Their robust design, high reliability, and ability to handle sudden load changes make them well-suited for powering inductive loads such as motors, pumps, and compressors. By following best practices for operating diesel generators, including proper sizing, regular maintenance, load testing, and fuel management, users can maximize the performance and reliability of their generators when powering inductive loads. Diesel generators will continue to be an essential resource for industries and businesses seeking reliable backup power solutions for their critical operations.